Blog
Is C10 the Right Barrier Fluid for your Seals?
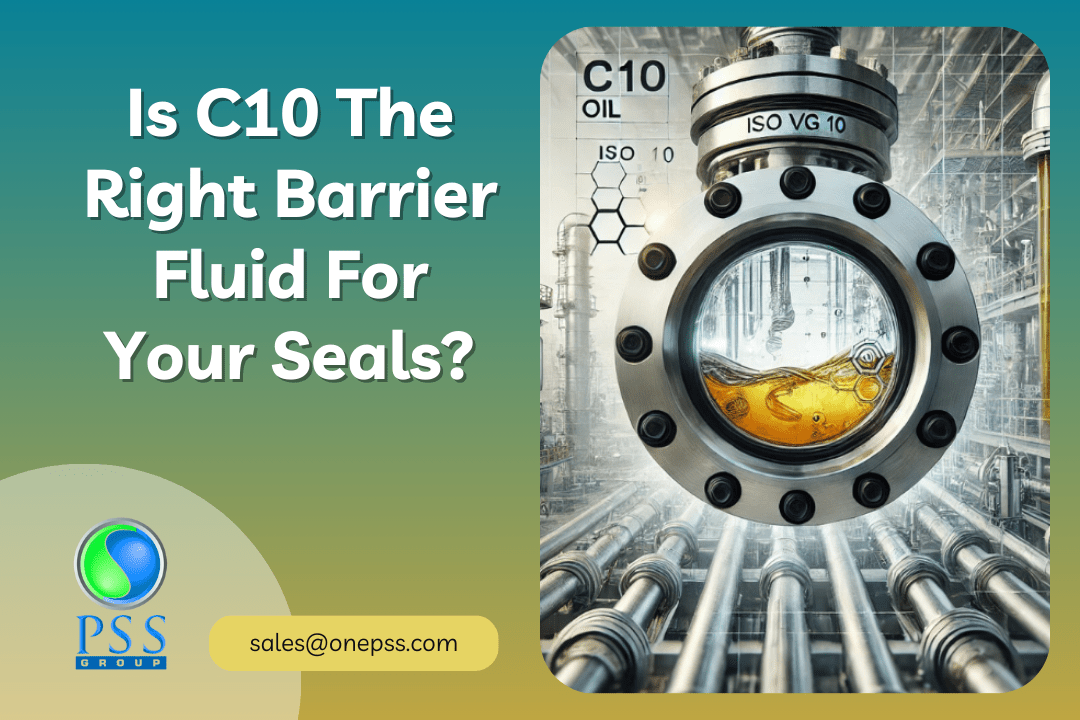
C10 oil (ISO VG 10) is widely used as a barrier fluid in API Plan 52 and 53 seal systems due to its low cost and availability. However, its low viscosity, high evaporation rate, and poor thermal stability make it unsuitable for many critical applications. Using C10 where it is not recommended can lead to excessive leakage, premature seal wear, and frequent top-ups—all of which increase maintenance costs and downtime.
Where is C10 Commonly Misapplied?
Many industries continue to use C10 in applications where a higher-viscosity or synthetic barrier fluid would be far more suitable. Below are key cases where C10 should not be used and what should replace it:
1. High-Temperature Pumps (>80°C) in Refineries & Petrochemicals
Example: Hot Amine Pumps, VGO Pumps, Heavy Oil Pumps
Why C10 Fails: Rapid evaporation and poor lubrication lead to frequent fluid loss and increased seal wear.
Better Alternative: C22, C32, or synthetic barrier fluids (PAO-based/PAG-based).
2. Boiler Feed Pumps & Steam Service Pumps
Example: KSB HGC5, Sulzer MC Series Pumps
Why C10 Fails: High temperatures cause fast degradation, requiring frequent refilling.
Better Alternative: C32 or synthetic high-temperature fluids.
3. LPG, Light Hydrocarbon, and Gas Pumps
Example: Propane, Butane, Naphtha Pumps in Gas Plants
Why C10 Fails: Low viscosity and high solubility in hydrocarbons reduce its effectiveness, leading to potential leaks.
Better Alternative: PAO-based synthetic fluids with high film strength.
4. Cryogenic Service (LNG, Liquid Oxygen, Liquid Nitrogen)
Example: LNG Loading Pumps
Why C10 Fails: Poor low-temperature properties—may solidify or become too thin.
Better Alternative: Specialized low-temperature barrier fluids.
5. High-Speed Equipment (Compressors & Turbines)
Example: Non-metallic labyrinth seals in centrifugal compressors
Why C10 Fails: Cannot maintain the necessary film thickness for high-speed seals.
Better Alternative: C22, C32, or synthetic oils with better shear stability.
6. Highly Corrosive Chemical Pumps
Example: Sulfuric Acid, Hydrofluoric Acid, Chlorinated Solvents
Why C10 Fails: Lacks sufficient chemical resistance and degrades upon exposure.
Better Alternative: Fluorinated oils or engineered synthetic fluids.
7. Gas-Sealed Plan 53C Systems
Example: Hydrogen or Gas Compression Applications
Why C10 Fails: High vaporization leads to poor gas barrier maintenance.
Better Alternative: PFPE-based or gas-compatible barrier fluids.
______________________________________________________________________________________________
What Should You Do?
If your facility currently uses C10 in these applications, it’s time to reassess your seal reliability strategy. Upgrading to the right barrier fluid can extend seal life, improve reliability, and reduce maintenance costs.