Blog
PSS CFD Study Reveals Critical Wear Risk in Absorber Recycle Pump
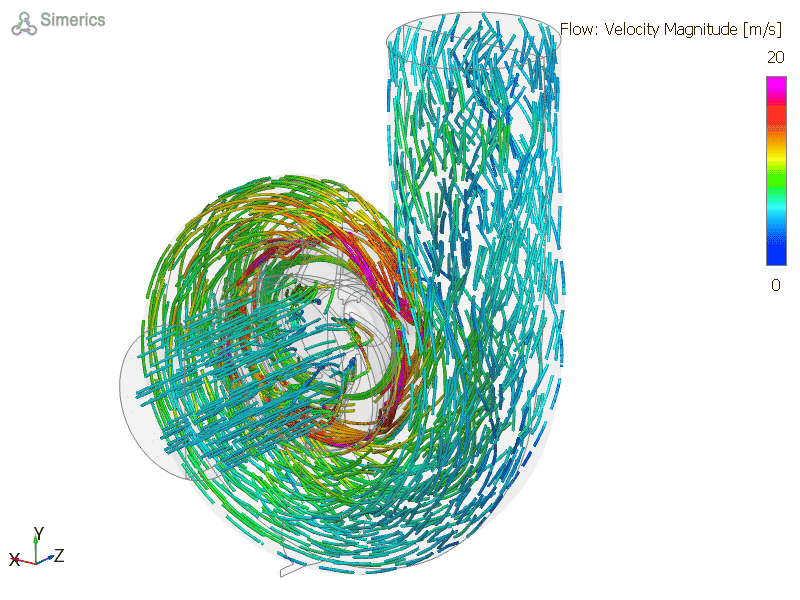
In critical services like absorber recycle pumps, small design flaws can lead to big reliability problems — especially in slurry handling environments with high solids and acidic exposure.
At PSS Group, we recently performed a complete reverse engineering and CFD validation on an absorber recycle pump as part of a refurbishment project for FGD service.
What we found highlights a problem that may be affecting many plants unknowingly — and one that we can help solve.
🔍 The Problem: Hidden High-Velocity Zone at the Cutwater
After 3D scanning the impeller, back cover, and casing using our FARO Arm and HandySCAN, we created full 3D models in CREO and ran Computational Fluid Dynamics (CFD) simulations to verify hydraulic performance.
✅ The pump curve matched the original
✅ No cavitation or flow separation was observed
⚠️ However, a concentrated high-velocity zone (~20 m/s) was found at the cutwater
In clear fluid, this may be tolerable — but in an absorber pump circulating gypsum and limestone slurry, this can cause:
- Rapid erosion near the cutwater
- Accelerated wear on volute casing
- Pressure pulsations and local turbulence
- Shorter Mean Time Between Failures (MTBF)
🧠 Our Engineering-Based Solution
Rather than replicating OEM geometry blindly, we delivered a solution based on field conditions and predictive simulation:
- Volute Geometry Review & CFD Validation:
We confirmed that flow was smooth, with no separation or instability — but high velocity at the cutwater posed a long-term wear risk. - Material Upgrade to ASTM A890 Grade 5A (Super Duplex):
We recommended upgrading the volute casing and impeller to cast Super Duplex 5A, offering:- Excellent resistance to erosion-corrosion in acidic slurry
- PREN > 40 for pitting resistance in chloride environments
- Better mechanical strength and wear life compared to CD4MCu or CR30A
- Coating or Local Reinforcement (Optional):
For clients who want added protection, we also recommend applying ceramic or polymer coatings near the high-wear zones identified in CFD.
💡 Why It Matters
Too often, pump overhauls focus only on dimensional restoration. But CFD allows us to visualize actual hydraulic risks and make engineering-based decisions that extend pump life and reduce unexpected failures.
When we combine:
- 3D scanning and modeling
- Predictive CFD simulations
- Smart materials and design modifications
… we don’t just repair pumps — we upgrade them for reliability.
📈 Talk to Us About Your Next Overhaul
If you’re planning an absorber pump repair or want to improve long-term reliability, our CFD-backed recommendations can reduce unplanned downtime and improve MTBF.