Gulf Coast Bearing & Seal
Thermoplastic Labyrinth Seals
For centrifugal compressors, GCBS designs and manufactures labyrinth seals – both stationary labyrinths and abradable designs. If you currently have stationary aluminum labyrinth seals, we can help you upgrade to composite labyrinth seals which can run with tighter clearances, increasing compressor efficiency and throughput.
Applying Thermoplastic Labyrinth Seals
Centrifugal compressors use labyrinth seals at the impeller eyes, between impellers, and at the balance drum. The purpose of the labyrinth seals is to reduce flow between stages; therefore, tight clearance and minimum flow between stages is an important factor in centrifugal compressor efficiency.
If you have a centrifugal compressor that was originally designed with stationary aluminum labyrinth seals, PSS can help together with the GCBS team. They have worked with OEMs, repair shops, and end users to upgrade hundreds of compressors from aluminum labyrinth seals to thermoplastic labyrinth seals. This simple change allows tighter clearance at the labyrinth seals, which will help increase your compressor efficiency and throughput.
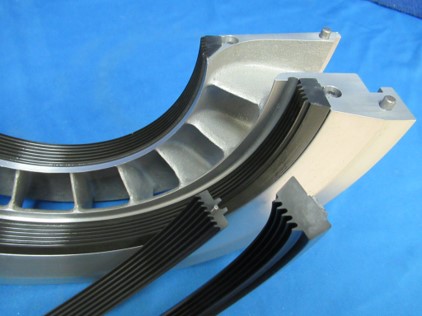
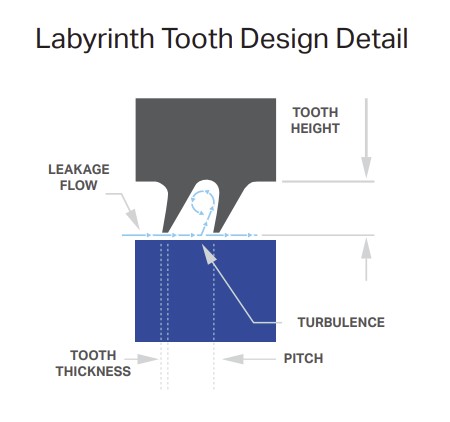
Key benefits of thermoplastic labyrinth seals:
- Non-seizing, non-galling material allows tighter running clearance
- Increased compressor flow rate
- Increased compressor efficiency
- Tolerant of transient contact at start-up
- Improved chemical resistance over aluminum
- Lower wear and longer life
Syngas plants can upgrade their syngas, ammonia, and air compressors. Ethylene crackers can upgrade their ethylene refrigeration, propylene refrigeration, and charge gas trains. Refineries can look at their wet gas, hydrogen recycle, and air compressors. Gas plants can consider any of their hydrocarbon compressors. If your centrifugal compressors are still using stationary aluminum labyrinth seals,